Alcast Company Fundamentals Explained
The Only Guide for Alcast Company
Table of ContentsSome Known Details About Alcast Company Excitement About Alcast CompanyLittle Known Questions About Alcast Company.Some Known Details About Alcast Company The 3-Minute Rule for Alcast CompanyThe 15-Second Trick For Alcast Company
Chemical Contrast of Cast Light weight aluminum Alloys Silicon advertises castability by minimizing the alloy's melting temperature level and boosting fluidness throughout casting. Furthermore, silicon adds to the alloy's strength and wear resistance, making it important in applications where durability is important, such as vehicle parts and engine elements.It likewise improves the machinability of the alloy, making it much easier to refine right into completed items. In this means, iron adds to the general workability of light weight aluminum alloys. Copper raises electric conductivity, making it helpful in electric applications. It likewise boosts rust resistance and contributes to the alloy's general stamina.
Manganese adds to the strength of aluminum alloys and boosts workability (aluminum metal casting). It is typically utilized in wrought light weight aluminum products like sheets, extrusions, and profiles. The visibility of manganese help in the alloy's formability and resistance to fracturing throughout construction procedures. Magnesium is a light-weight aspect that provides stamina and impact resistance to aluminum alloys.
The Ultimate Guide To Alcast Company
It allows the manufacturing of lightweight elements with excellent mechanical homes. Zinc boosts the castability of aluminum alloys and assists control the solidification procedure throughout casting. It boosts the alloy's strength and hardness. It is typically located in applications where intricate shapes and great information are necessary, such as ornamental castings and particular automotive parts.
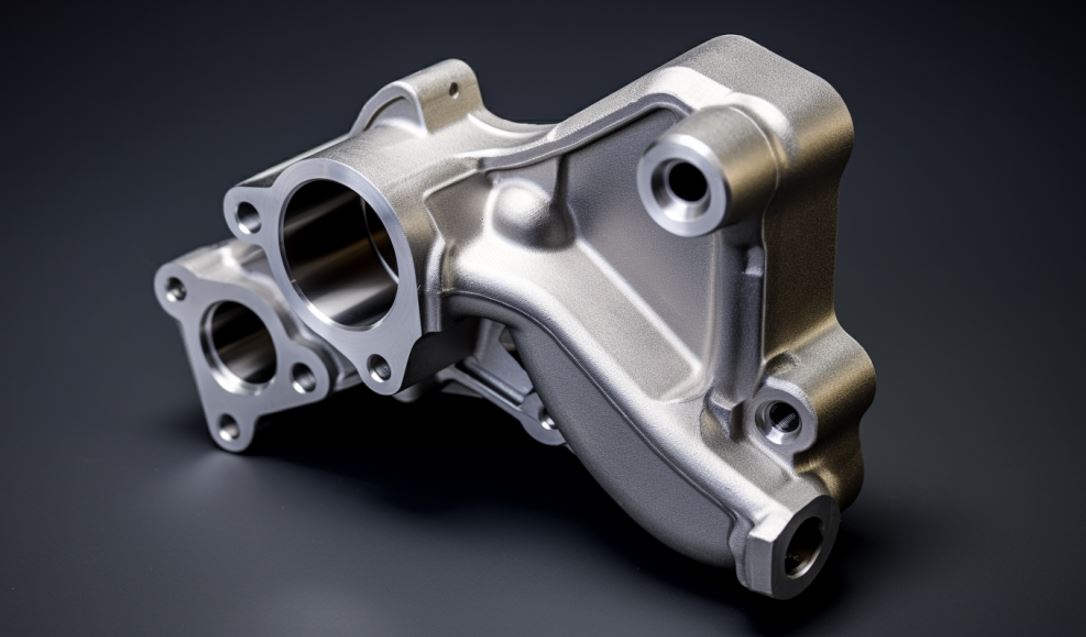
The key thermal conductivity, tensile strength, return strength, and elongation differ. Select ideal resources according to the performance of the target product created. Among the above alloys, A356 has the highest possible thermal conductivity, and A380 and ADC12 have the most affordable. The tensile restriction is the opposite. A360 has the very best return strength and the highest elongation rate.
How Alcast Company can Save You Time, Stress, and Money.
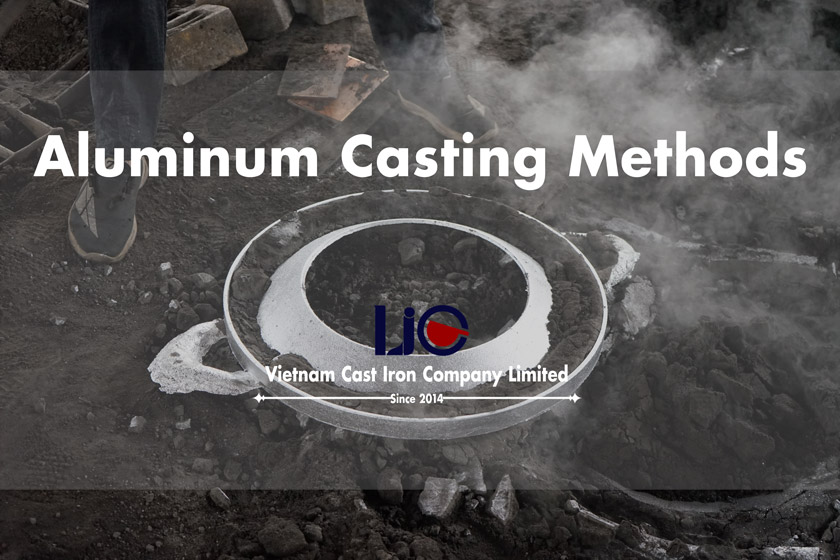
In accuracy casting, 6063 is well-suited for applications where elaborate geometries and high-quality surface finishes are extremely important. Examples consist of telecommunication rooms, where the alloy's remarkable formability allows for smooth and cosmetically pleasing layouts while maintaining structural honesty. In the Lighting Solutions market, precision-cast 6063 elements produce stylish and reliable lighting fixtures that require complex shapes and great thermal efficiency.
The A360 displays remarkable elongation, making it optimal for complicated and thin-walled elements. In accuracy casting applications, A360 is appropriate for industries such as Customer Electronic Devices, Telecommunication, and Power Devices.
Alcast Company Things To Know Before You Get This
Its one-of-a-kind residential or commercial properties make A360 a useful option for accuracy spreading in these sectors, enhancing product sturdiness and quality. Casting Foundry. Aluminum alloy 380, or A380, is a widely utilized casting alloy with several distinctive attributes.
In accuracy spreading, light weight aluminum 413 beams in the Customer Electronics and Power Tools industries. It's commonly used to you can try this out craft detailed elements like smart device real estates, electronic camera bodies, and power device cases. Its precision is amazing, with tight tolerances up to 0.01 mm, guaranteeing flawless item assembly. This alloy's exceptional rust resistance makes it an outstanding choice for outside applications, ensuring long-lasting, sturdy products in the pointed out industries.
See This Report on Alcast Company
The aluminum alloy you choose will considerably influence both the casting process and the properties of the final product. Since of this, you need to make your choice carefully and take an informed method.
Establishing the most appropriate aluminum alloy for your application will suggest weighing a broad range of qualities. These comparative alloy features follow the North American Die Casting Association's standards, and we have actually separated them into 2 categories. The first category addresses alloy qualities that influence the production procedure. The second covers qualities impacting the residential properties of the last product.
More About Alcast Company
The alloy you choose for die spreading straight influences a number of facets of the casting procedure, like exactly how easy the alloy is to function with and if it is vulnerable to casting flaws. Hot fracturing, also called solidification splitting, is a typical die spreading defect for light weight aluminum alloys that can lead to inner or surface-level rips or splits.
Certain aluminum alloys are extra vulnerable to hot splitting than others, and your selection ought to consider this. An additional common defect discovered in the die spreading of light weight aluminum is die soldering, which is when the actors sticks to the die walls and makes ejection tough. It can damage both the cast and the die, so you ought to try to find alloys with high anti-soldering residential properties.
Corrosion resistance, which is already a remarkable attribute of aluminum, can differ substantially from alloy to alloy and is an essential characteristic to take into consideration depending upon the ecological problems your product will be exposed to (Casting Foundry). Put on resistance is another property commonly looked for in light weight aluminum items and can separate some alloys